BackNews
Wear resistance of refractories in practical applications
2020-05-18 16:58:13The wear resistance of refractory materials is their ability to resist the mechanical abrasion of solid, liquid and dust-containing airflow on their surfaces.
In many cases, the damage caused by mechanical wear on the surface of refractory materials is often very serious. It is often the direct cause of loss of refractory material from its working surface. Sometimes it is more harmful than chemical attack, or the damage caused by chemical attack is often exacerbated by mechanical action. For example, the refractory lining and molten iron ditch in the upper part of the blast furnace are often worn out due to insufficient wear resistance. Refractory materials in the coking oven coking chamber are also susceptible to coke wear. The furnace openings, steel outlets of steel-making converters, and other places where air currents scour and various melts flow through are often lost due to poor wear resistance of the materials. Therefore, the wear resistance of refractory materials is an important property.
Refractory wear resistance depends on the composition and structure of the material. When the material is a dense multi-crystal composed of a single crystal, its wear resistance mainly depends on the hardness of the mineral crystals constituting the material. High hardness and high wear resistance of the material. When the mineral crystals are non-isotropic, the grains are fine and the wear resistance of the material is high. When the material is composed of multiple phases, its abrasion resistance is also directly related to the bulk density or porosity of the material, as well as the bonding strength of each component.
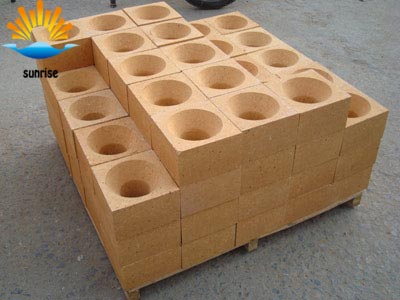
Therefore, for a certain refractory material at normal temperature, its wear resistance is proportional to its compressive strength, and a good sintered product has better wear resistance. The abrasion resistance of refractory products is related to temperature. Some materials such as silicon aluminum refractory products are generally considered to be at a certain temperature (such as within the elastic range of 700 ~ 900 ℃), the higher the temperature, the lower the wear resistance, you can think that when the temperature increases, the elasticity As the modulus increases, the wear resistance decreases.
When the temperature increases and reaches the maximum value of the elastic modulus, as the elastic modulus decreases, the wear resistance increases. Such as aluminum silicate refractory products at 1200 ~ 1350 ℃, the wear resistance is even better than those at room temperature. When the temperature is further increased to more than 1400 ℃, the liquid phase viscosity in the refractory products decreases sharply, and the wear resistance decreases accordingly. Some refractory materials, such as chromium products, increase in wear resistance as the temperature increases.