Preparation and performance index of aluminum carbon brick for blast furnace
2020-01-03 15:20:49
Refractory aggregates and powders are mainly made of super-grade and first-grade alumina clinker, and white corundum and brown corundum can also be used; carbon materials are mainly used in flake graphite, and medium-temperature asphalt polysilicon is used in super or first grade Available phenolic resin for dense sic binder, its solid content is ≥75%, free phenol is ≤6%, residual carbon content is ≥43%, water content is ≤2%, density is about 1.1g / cm. The critical diameter of the refractory aggregate for this brick is 8mm, and its general mixing ratio is: coarse aggregate 40% ~ 60%, fine aggregate 5% ~ 20%, flake graphite 8% ~ 15% SiC 4% ~ 10%, fire resistance 15% ~ 25% powder and 4% ~ 6% binder. In addition, additives such as ultrafine powder, anti-alkali agent and bulking agent are added as needed.
The technical measures of aluminum carbon bricks are multi-grade gradation of refractory aggregates. Pre-mixed powders are made of additives or solid binders and refractory powders, and appropriate amounts of additives are added at the same time. When mixing the materials, first add the granules and binders. After the granules are completely wrapped by the binders, add various powders and mix for 15 ~ 20min. In 10 times. The larger the tonnage of the brick press, the less the number of presses, but at least 5 times. At the same time, the operation should be light first and then heavy to facilitate exhaust and reduce cracks.
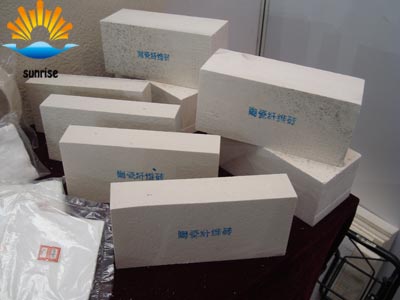
After molding the semi-finished products, check the appearance, size and quality. The semi-finished products that pass the inspection are put into an inverted flame kiln for baking and curing, and can be heated directly or indirectly. The firing curing temperature depends on the type of binder, generally 20250, and the firing time is usually 20 s50h. Among them, the resin begins to soften at 50 ~ 60C, and the solvent in the resin is excluded at 100, so it should be properly maintained. When the curing temperature is reached, the reaction should also be properly maintained in order to complete the reaction and form a carbon bond. Of course, the final formation of carbon bonds occurs at higher temperatures. The products out of the kiln should be stacked in the warehouse, or temporarily stored in the open air.