BackNews
Analysis of the difference between fused brick and clay brick
2019-10-31 15:49:37The fused silica brick is a white solid formed by purifying the pure alumina powder and zircon sand containing about zirconia 65% and about 34% of silica in an electric melting furnace and then injecting it into a mold. The lithofacies structure consists of an eutectoid and a glass phase of corundum and zirconium, which are phased as eutectoids of the corundum phase and the zircon oblique phase, and the glass phase is filled between their crystals.
Artificial small blocks for construction, also known as sintered bricks. Clay bricks are made of clay (including shale, coal gangue and other powders), processed by mud, shaped, dried and calcined. During the Spring and Autumn Period and the Warring States Period, China successively created square and long-shaped bricks. The technology and production scale, quality and fancy varieties of brick making in the Qin and Han Dynasties have developed significantly. The world is called “Qin Brick Hanwa”. The size of ordinary brick is 240mm × 115mm × 53mm, divided into MU30, MU25, MU20, MU15, MU10, MU7.5 according to the compressive strength (Newton / square millimeter, N / mm2), 6 intensity levels .
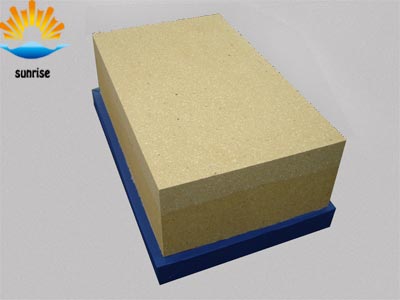
Clay bricks are made in situ, cheap, durable, and have the advantages of fire prevention, heat insulation, sound insulation, moisture absorption, etc., and are widely used in civil engineering construction. Waste bricks can also be used as aggregates for concrete. In order to improve the shortcomings of ordinary clay bricks, self-importance and soil consumption, the development of light, high strength, hollow and large blocks is progressing. The lime sand brick is formed by grinding and mixing the lime and quartz sand, sand or fine sandstone in an appropriate proportion, mixing with water, semi-dry pressing and autoclaving. Fly ash brick uses fly ash as the main raw material, and is mixed with coal gangue powder or clay and other cementing materials. After being compounded, shaped, dried and calcined, it can make full use of industrial waste residue and save fuel.
The content of Al2O3 in clay bricks in China is generally more than 40%, and the content of Fe2O3 is less than 2.0 to 2.5%. The clinker in the furnish is 65-85%, and the combined clay is 35-15%. The pulverized bonded clay and the ground clinker are mixed and ground, and then combined with the granular clinker to prepare a semi-dry mud, which is formed by high pressure molding and fired at about 1400 ° C, and has good performance. Clay bricks are weakly acidic at high temperatures and have a slightly poorer ability to resist alkaline slag, but increase with increasing Al2O3 content. The thermal stability is better than that of silica bricks and magnesia bricks (see magnesia bricks).