BackNews
Technical Requirements for Sunrise Refractory Fused Zirconium Corundum Brick
2019-06-18 16:41:56The fused zirconia corundum brick is a white solid formed by pure alumina powder and zircon sand containing zirconia of 65% and about 34% of silica in the electric melting furnace and then injected into the mold to be cooled. The structure consists of an eutectoid and a glass phase of corundum and zirconium, which are phased as eutectoids of the corundum phase and the zircon oblique phase, and the glass phase is filled between their crystals.
Electrofusion brick melting technology requirements:
(1) The long arc method is used for the melting process, and the secondary voltage is controlled between 320 and 380 volts. The initial stage of melting is melted with a high voltage, the secondary voltage is 380 volts, the secondary voltage during the refining period is controlled at 320 volts, and the arc length must be 50-60 mm.
(2) Current selection: At the initial stage of melting, the current should be controlled at 3500-4000 amps, and pay attention to the change of three-phase electrode current at any time, try to maintain balance, the current can be increased during refining, using high current refining, current control at 4500 Ann.
(3) Melting time: The melting time per furnace is about 150 minutes, in which it is melted for 120 minutes and refined for about 30 minutes.
(4) Oxygen blowing: oxygen is sprayed in a stepwise manner, and oxygen is blown twice per furnace. The oxygen pressure is 1.4-1.6 MPa. When oxygen is blown, the oxygen lance should be inserted into the 1/2 of the depth of the liquid and shake slowly. The oxidation is sufficient.
(5) The casting temperature is 1850-1950 °C, and the winter must be above 1950 °C.
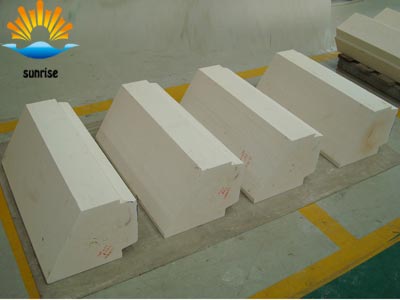
Casting technical requirements:
(1) When casting, the furnace body should be inclined at a uniform speed and keep flowing. Follow the principle of “slow first, fast in the middle, and finally slow” to avoid empty shells and pores.
(2)After casting, the depth of the remaining liquid in the furnace shall not be less than 180 mm.
(3) Master the time and strength of the processing of the casting nozzle, and the convexity and concave of the casting mouth should meet the internal control standard.