BackNews
The Development and Improvement of China 's Refractory Material Production Equipment
2017-09-25 10:10:481. Semi-dry method to update the foreign design of the plastic and wet process
At the beginning of the founding of the Soviet Union, the United States for the Anshan Iron and Steel clay plant renovation process, the design of the Central Plains using plastic molding, with "Spitzwalk" forming steel bricks, at the time is still advanced technology, but the plastic has its inherent shortcomings, Consumption of the complex and the products of high stomatal and low strength, the domestic design to use semi-dry method, and designed to meet the semi-dry molding requirements of the friction press, not only save energy consumption and improve product quality, But also save the construction of a number of dryer investment and plant.
The Soviet Union for the Dashiqiao magnesia brick factory designed magnesium sanding process using a mud method. The main drawback of this process is the large energy consumption, low kiln utilization factor and the need for large capacity mud as the concentration and storage slurry. After the success of semi-dry calcination in the grate on the cement rotary kiln with powder into the ball, the wet calcination was changed to the more advanced semi-dry process, and the economic effect was remarkable.
2. The use of synthetic process, calcined magnesia, high-alumina raw materials
Synthetic raw material calcination process has the advantage of making full use of crushed ore, mixed material uniform raw material ingredients, and according to the requirements of ingredients, the production of multi-species synthetic materials. Dashiqiao magnesium brick factory large cylinder mill before the multi-trough ingredients, powder into the ball calcined, is the effective synthesis of the process. 1978 Yangquan bauxite mine for the first time using compressed air in the trough mixed powder and ball into the ball into the ball process, can be uniform grade of raw materials, especially for the use of mine mixed material, but also adjust the different components, artificial synthesis, and now High bauxite homogenization of industrialization in our country in the ascendant. In recent years, southern Liaoning region using synthetic process, rotary kiln calcined production of synthetic varieties of chromium chrome sand, magnesium calcium sand and magnesia sand and so on. Synthetic synthetic weighing, mixing ingredients, molding and high temperature calcination equipment put forward new requirements.
3. A New Technology of Making Pear Dolomite Brick by Vibration Forming
The products have the advantages of strong anti-hydration ability, low lining of lining lining, and strong anti-impact, anti-impact and anti-corrosion resistance, Erosion and erosion resistance. In addition, it has the advantages of high labor productivity during the molding process and the overall suspension of the masonry, the operation is relatively simple and the speed of the blast furnace is accelerated. The effect of the blast furnace is achieved in the practice of converter steelmaking. In our country has not yet widely used high-tonnage hydraulic machine under the conditions of the development of China's tar asphalt as a binder alkaline lining brick, in the late 1960s to the 1970s, with converter steel furnace age, with a certain Practical significance.
4. High-purity alkaline materials, using two-step calcination of new technology
The two-step calcination process in the production of seawater magnesia is transplanted into the calcination process of magnesium and calcium alkaline refractory raw materials. The process has the advantages of activating raw material lattice, reducing sintering temperature, improving material density and facilitating artificial synthesis. Some of China's basic raw materials of pure, difficult to sintering the problem. The late 70s, the domestic general promotion of two-step calcination of new technology since the sizing of high-quality alkaline raw materials is a breakthrough. The processing of magnesite in Haicheng is made up of 98% of MgO with fine grinding, light burning, pressing and sintering, and has been put into mass production.
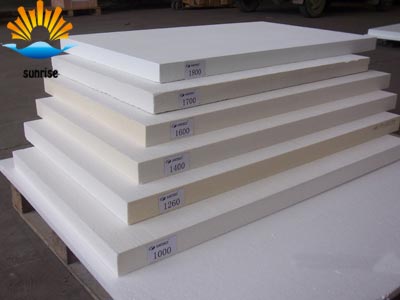
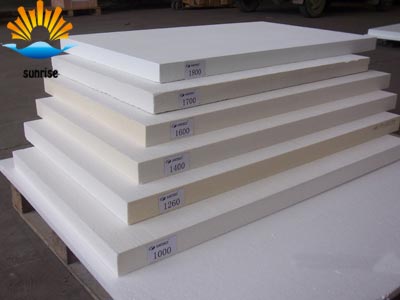